The Hidden Costs of Unsafe Warehousing: A Guide to Insurance Implications
The Hidden Costs of Unsafe Warehousing: A Guide to Insurance Implications
Did you know there’s a significant connection between warehouse safety and insurance? The relationship between these two elements is complex, and managing them effectively can lead to substantial benefits. In this article, we’ll explore how a lack of safety commitment can impact insurance coverage for warehouses and provide actionable strategies to create a resilient, financially protected operation. We’ll focus on key areas such as training, inspections, and the integrity of pallet racking systems, all of which play a crucial role in insurance considerations.
The Hidden Costs of Compromised Safety
According to a recent study, being a warehouse operative ranks as one of the most dangerous occupations in the UK. This statistic underscores the importance of safe working practices, which are closely tied to insurance coverage. From an insurer’s perspective, unsafe warehousing poses a significant financial risk. The implications extend far beyond the potential for accidents; they can jeopardise the financial health of the entire operation. By understanding the link between safety and insurance, you can adopt a practical approach to mitigate risks and foster positive insurance outcomes.
Let’s delve into how unsafe warehousing affects insurance coverage, premiums, and limitations.
Insurers’ Perspectives on Unsafe Warehousing
Unsafe warehousing translates to hazardous working conditions. From an insurer’s viewpoint, this can lead to several consequences:
Heightened Risk Perception: Insurers assess risk levels when determining premiums. If unsafe practices indicate a higher likelihood of incidents, expect increased premiums.
Increased Probability of Claims: Unsafe environments are prone to accidents and injuries. Insurers anticipate more frequent claims, resulting in higher premiums.
Significant Payouts: Injuries or damage in unsafe conditions tend to be more severe, impacting the overall cost of coverage.
Poor Loss History: Insurers evaluate loss history; a high frequency of claims due to unsafe conditions can adversely affect premiums and coverage.
Non-Compliance with Safety Regulations: Failure to comply with safety regulations can lead to increased premiums and limited coverage.
Potential Policy Exclusions: A history of unsafe practices may result in safety-related incidents being excluded from the policy, increasing financial exposure.
Refusal of Coverage: Warehouses that consistently prioritize unsafe practices may struggle to obtain coverage, placing the business in a vulnerable financial position.
Lack of Employee Liability Coverage: A higher risk of employee injury may limit coverage options. Conversely, prioritising safety can lead to lower premiums and better coverage.
Actionable Strategies for a Safe and Insurable Warehouse
Transforming your warehouse from a risk-laden environment to a secure one requires a comprehensive approach to safety and risk management. Here are some strategies to help you create a safer, insurable warehouse:
1. Initiate a Detailed Safety Review:
Conduct a thorough assessment to identify potential hazards within your warehouse. Analyze every aspect of your operation, including racking systems, warehouse layouts, structural issues, staff training, fire safety, and records of past incidents. In some cases, insurers may recommend an on-site risk survey conducted by their surveyor.
2. Categorise Defined Risks:
Once hazards are identified, categorize them:
Equipment Malfunctions: Issues such as forklift failures or pallet racking overloads can lead to incidents.
Operational Risks: Inadequate safety training or poor workflow design can increase risks, leading to collisions or blockages.
Physical Hazards: Risks like falling objects from racking or inadequate pedestrian walkways should be addressed.
3. Undertake a Severity Assessment:
Evaluate the potential impact of each identified risk on employee safety and warehouse infrastructure.
4. Consider Probability of Occurrence:
Utilise historical incident data, current procedures, and training standards to establish the likelihood of a risk becoming an actual incident.
5. Create a Risk Priority Chart:
Develop a risk matrix that considers the likelihood of incidents, severity levels, compliance regularity, and potential liability. Share and discuss this matrix with your health and safety team to collaboratively address identified hazards.
Implementing Immediate Actions and Long-Term Strategies
Once potential risks are identified, you can address them through immediate actions and long-term strategies:
Immediate Actions:
Conduct regular emergency evacuation drills to familiarise employees with procedures.
Ensure emergency equipment, like fire extinguishers and first aid kits, are easily accessible.
Schedule a professional racking inspection if it’s been over a year since the last check or if there are visible concerns.
Display warning signs and secure dangerous areas with barriers.
Long-Term Strategies:
Optimise warehouse layout for better flow and accessibility.
Establish an annual schedule for racking inspections to maintain compliance with safety regulations.
Provide racking inspection training for staff to enable in-house checks throughout the year.
Ensure fire marshal and first aid training is conducted for personnel from various shifts to maintain competence.
Choose a Trade Body Trusted provider for your storage solutions, as this can positively influence insurers. Selecting a Full SEMA Member ensures adherence to best practices and safety standards.
Regular Reviews
Conduct incident reviews to investigate any safety incidents thoroughly, documenting all findings. This process will help establish root causes and offer opportunities to improve safety protocols.
Regularly assess training effectiveness to identify gaps in employee knowledge and experience, ensuring relevant training programs are implemented.
Stay informed about regulations by checking the Health and Safety Executive (HSE) website for updates and engaging with industry professionals.
Perform regular safety audits, covering various protocols, including emergency procedures, fire safety, equipment usage, and personal protective equipment (PPE).
Prioritise safety when introducing innovations like automation and robotics, ensuring compliance with layout design, regulations, and training.
Conclusion
Prioritising warehouse safety is not just a moral obligation; it can lead to significant improvements in insurance outcomes. By demonstrating a long-term commitment to high safety standards, you can avoid increased premiums, limited coverage, or even refusal of coverage. Instead, insurers will view your operation as a lower risk, offering better coverage and terms.
If you’re looking to enhance your warehouse safety, A-Z Storage Systems can assist in various ways, from optimising layouts to inspecting racking structures. We can also provide training sessions to empower your team to conduct internal inspections. For peace of mind and a safer warehouse, contact us today at 07917 664940 or email sales@a-zstoragesystems.co.uk.

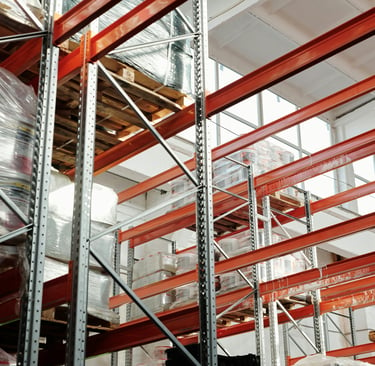
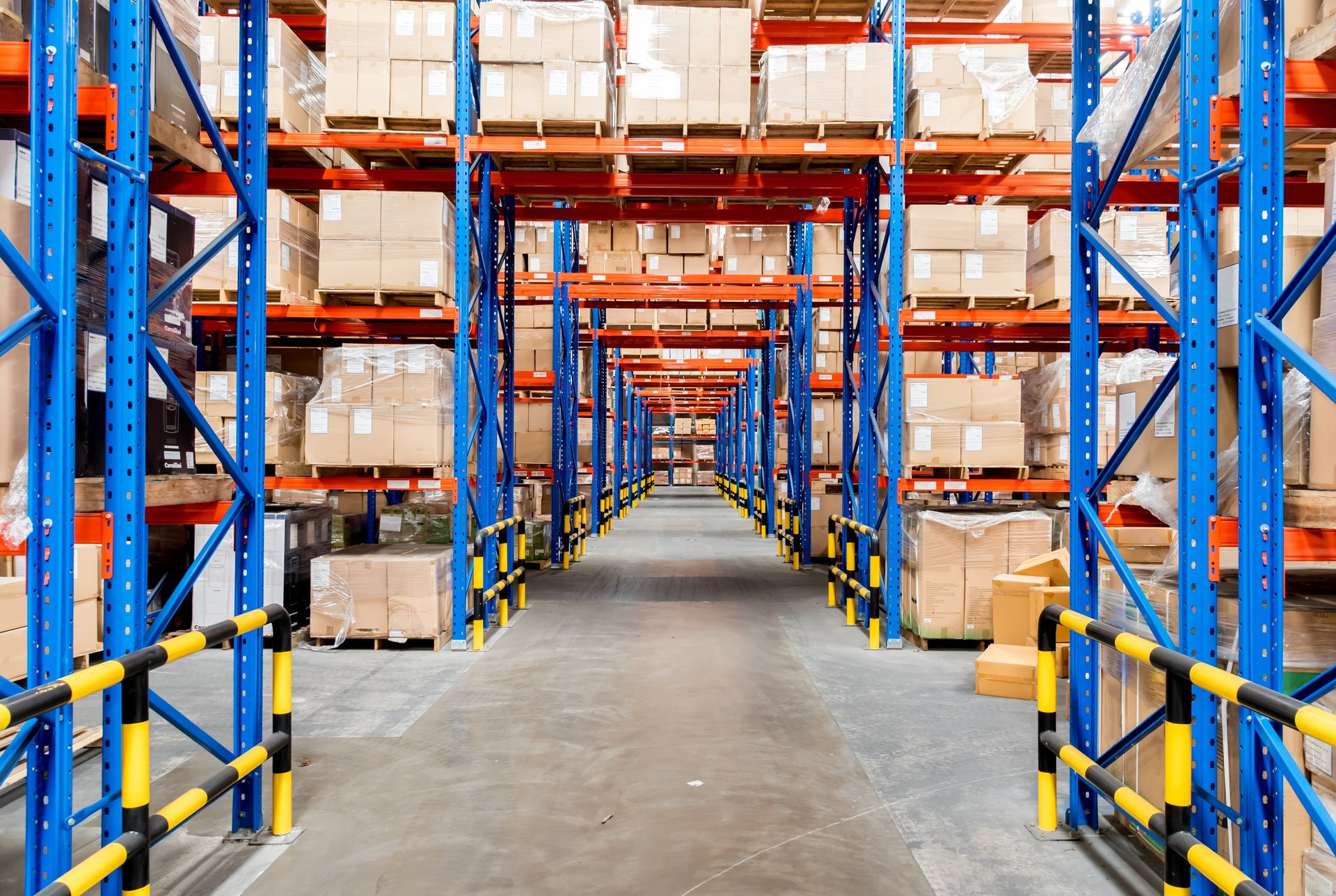
To discuss your requirements, find out more about our range of storage solutions and services, or arrange a FREE site visit please get in touch.
Call us on 07917 664940 or email us at sales@a-zstoragesystems.co.uk