Maximising Warehouse Efficiency: Strategies for Optimising Space and Storage
Maximising Warehouse Efficiency: Strategies for Optimising Space and Storage
In the fast-evolving world of logistics and supply chain management, efficient warehouse operations are critical for ensuring timely deliveries, minimising costs, and boosting customer satisfaction. A key component of achieving operational excellence is the effective utilisation of warehouse space and storage solutions. By optimising these elements, businesses can streamline processes, reduce waste, and enhance productivity. This blog explores practical strategies to improve warehouse efficiency through better space management and storage optimisation.
Conduct a Comprehensive Space Audit
The first step in optimising warehouse space is to thoroughly assess the current layout and storage systems. Identify inefficiencies such as underutilised spaces, crowded aisles, or poorly organised shelving. Use digital mapping tools or warehouse management software to visualise the layout and pinpoint areas for improvement. If you need assistance, our team specialises in maximising space utilisation, no matter the layout (click here for a warehouse design service).
Implement Vertical Storage Solutions
Maximize your storage capacity by investing in vertical storage solutions, such as pallet racking systems, mezzanine floors, or automated storage and retrieval systems (AS/RS). These options take advantage of overhead space, allowing for more inventory storage within the same footprint. Additionally, consider adjustable shelving units that can be customised to accommodate different inventory sizes and shapes.
Adopt Lean Inventory Management Practices
Lean inventory management is key to minimising waste and optimising storage space. Conduct regular inventory audits to identify and remove slow-moving or obsolete items. Implement a just-in-time (JIT) inventory system to align stock levels with actual demand, reducing excess inventory and storage costs.
Utilise FIFO and LIFO Inventory Methods
Implement first-in, first-out (FIFO) or last-in, first-out (LIFO) inventory management principles to ensure efficient stock rotation and minimise the risk of obsolescence or spoilage. Organise inventory to facilitate easy access to older stock, minimising unnecessary handling and ensuring timely use.
Optimise Pick-and-Pack Processes
Enhance the efficiency of pick-and-pack operations by organising inventory according to movement frequency and order-picking patterns. Group frequently picked items in dedicated zones to reduce travel time and increase picking speed. Use slotting optimisation techniques to position fast-moving items closer to packing stations.
Invest in Space-Saving Technologies
Incorporate advanced technologies such as warehouse robotics, conveyor systems, and automated guided vehicles (AGVs) to improve space utilisation and streamline material handling. These technologies can reduce the reliance on manual labour, increase throughput, and minimise errors associated with manual processes.
Embrace Cross-Docking and Consolidation
Implement cross-docking and consolidation strategies to reduce storage needs and streamline logistics. By transferring goods directly from receiving to shipping, businesses can minimise inventory holding times and expedite order fulfilment.
Conclusion
Optimising warehouse space and storage is crucial for enhancing operational efficiency and maintaining a competitive edge in today’s dynamic business environment. By conducting a comprehensive space audit, implementing vertical storage solutions, adopting lean inventory practices, optimising pick-and-pack processes, investing in space-saving technologies, and embracing cross-docking and consolidation, businesses can drive sustainable growth and success.
For more personalised assistance in optimising your warehouse space, feel free to contact us. We're here to help!


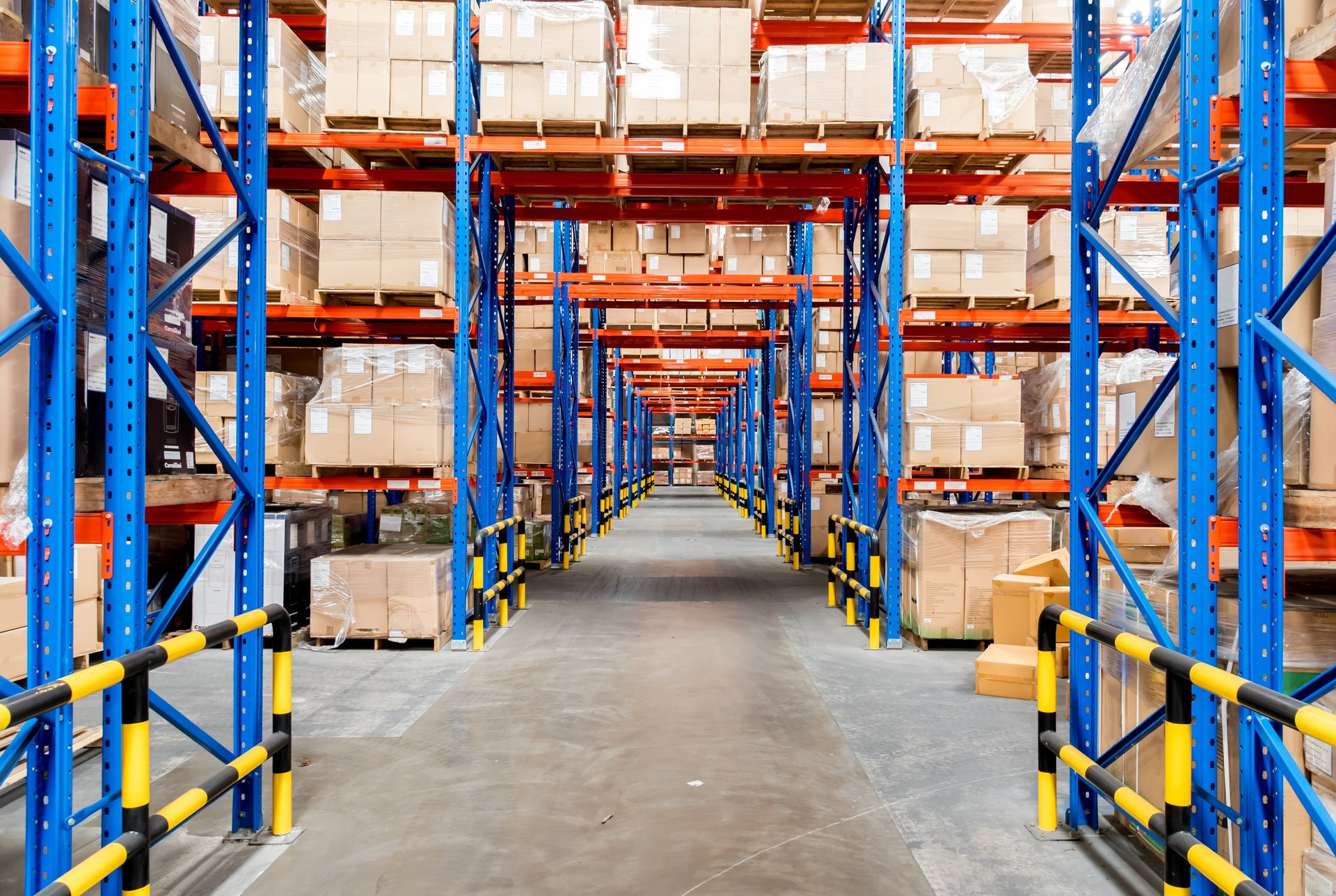
To discuss your requirements, find out more about our range of storage solutions and services, or arrange a FREE site visit please get in touch.
Call us on 07917 664940 or email us at sales@a-zstoragesystems.co.uk