How to Choose the Right Racking System for Your Warehouse
How to Choose the Right Racking System for Your Warehouse
Selecting the right racking system for your warehouse is crucial to maximising storage capacity, ensuring efficient operations, and maintaining safety standards. With a wide range of racking systems available, understanding the differences and benefits of each is essential to making an informed decision. In this blog post, we’ll discuss the most common types of warehouse racking systems and how to choose the one that best suits your needs.
Overview: Pallet racking is one of the most widely used systems in warehouses and distribution centres. It is designed to store palletised goods in horizontal rows with multiple levels, maximising the use of vertical space.
Types of Pallet Racking:
Adjustable Pallet Racking: Provides easy access to all pallets and is highly versatile. Ideal for warehouses with a large variety of products that need regular access.
Double-Deep Pallet Racking: Pallets are stored two deep, which increases storage capacity but may require specialised equipment for accessing rear pallets.
Best for: Warehouses that handle a wide range of products with varying turnover rates and require immediate access to inventory.
Overview: Cantilever racking is designed for storing long, bulky items such as timber, pipes, and steel bars. It features arms that extend from a central column, allowing for open-front storage.
Benefits: This system allows for flexible storage of long materials without any vertical obstructions. It is easy to load and unload with forklifts.
Best for: Warehouses that need to store long, oversized items that do not fit on traditional pallet racking.
Overview: Drive-in pallet racking allows forklifts to drive directly into the lanes to load and retrieve pallets. This system is based on a Last-In, First-Out (LIFO) inventory management system, where the last pallet placed in the racking is the first to be retrieved.
Benefits: It maximises storage density, making it ideal for storing large volumes of homogeneous products.
Best for: Warehouses that store large quantities of the same item and prioritise storage space over product accessibility.
Push-Back Racking
Overview: Push-back racking stores pallets on a series of nested carts that operate on inclined rails. When a pallet is loaded, it pushes the pallet behind it, and when it is removed, the next pallet automatically moves forward.
Benefits: Increases storage density and allows for Last-In, First-Out (LIFO) inventory management without the need for special handling equipment.
Best for: Warehouses with medium to high turnover rates and multiple pallets of the same product.
How to Choose the Right Racking System
When selecting the best racking system for your warehouse, consider the following factors:
Storage Needs
Product Size and Weight: Different racking systems cater to different sizes and weights of products. Cantilever racking is perfect for long, heavy items, while pallet racking is ideal for palletised goods.
Inventory Turnover: If you need quick access to a variety of products, selective pallet racking may be the best option. However, if you’re dealing with high volumes of the same product, drive-in racking or push-back racking could be more suitable.
Warehouse Space and Layout
Available Floor and Vertical Space: Assess how much floor and vertical space you have. Systems like pallet racking and cantilever racking allow for optimal use of vertical space, while drive-in racking maximizes floor space usage.
Aisle Width: Wide aisles are necessary for selective pallet racking, while narrow aisles can accommodate drive-in or push-back racking to increase storage density.
Accessibility Requirements
Picking and Loading Frequency: If your warehouse operations require frequent loading and picking, selective pallet racking offers direct access to all products. On the other hand, systems like drive-in racking limit access but offer better space efficiency.
FIFO or LIFO: Choose a system that supports your inventory management needs. For example, drive-in racking supports LIFO.
Safety and Compliance
Ensure your chosen racking system complies with safety regulations, such as SEMA standards, and is regularly inspected by qualified professionals. Racking safety inspections should be part of your warehouse maintenance routine to prevent accidents and ensure long-term durability.
Budget
Installation and Maintenance Costs: Some racking systems, such as selective pallet racking, are more affordable to install and maintain, while others, like push-back or carton flow racking, may involve higher upfront costs but provide long-term efficiency gains.
Conclusion
Choosing the right racking system for your warehouse is a critical decision that impacts storage efficiency, safety, and operational performance. By understanding the strengths and weaknesses of various systems—whether it’s pallet racking for versatile storage, cantilever racking for long items, or drive-in racking for maximum density—you can make an informed decision based on your specific needs.
For expert racking repairs and maintenance, or if you're considering new racking installations, trust A-Z Storage Systems to provide high-quality service and support. Contact us today to ensure your pallet racking system remains in optimal condition!


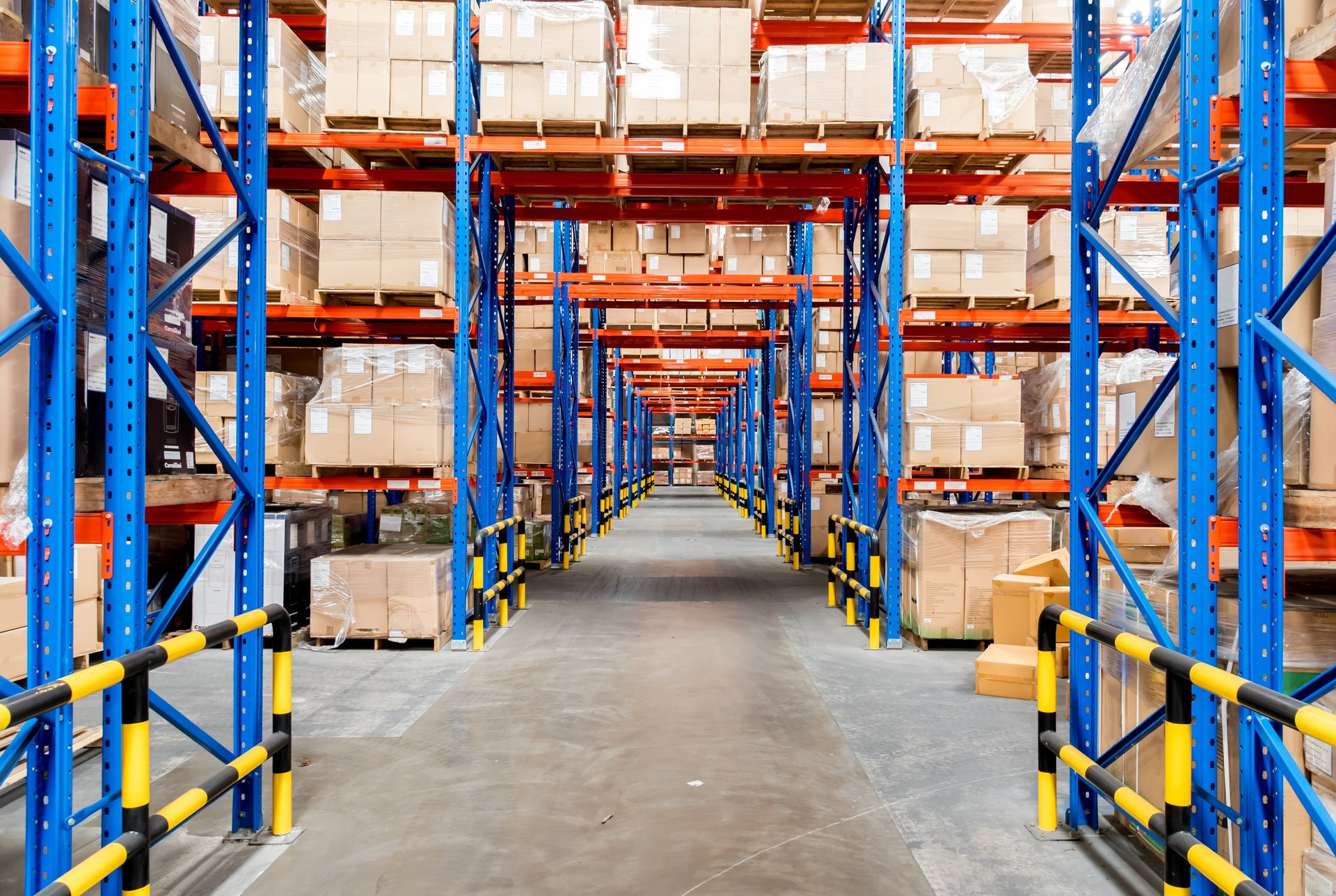
To discuss your requirements, find out more about our range of storage solutions and services, or arrange a FREE site visit please get in touch.
Call us on 07917 664940 or email us at sales@a-zstoragesystems.co.uk